The Evolution of Stone Cage Net Machines: From Manual Crafting to Automated Production
- Share
- Issue Time
- Nov 30,2023
Summary
This article traces the evolution of these machines, reflecting on past practices and celebrating modern advancements that have redefined efficiency and productivity.
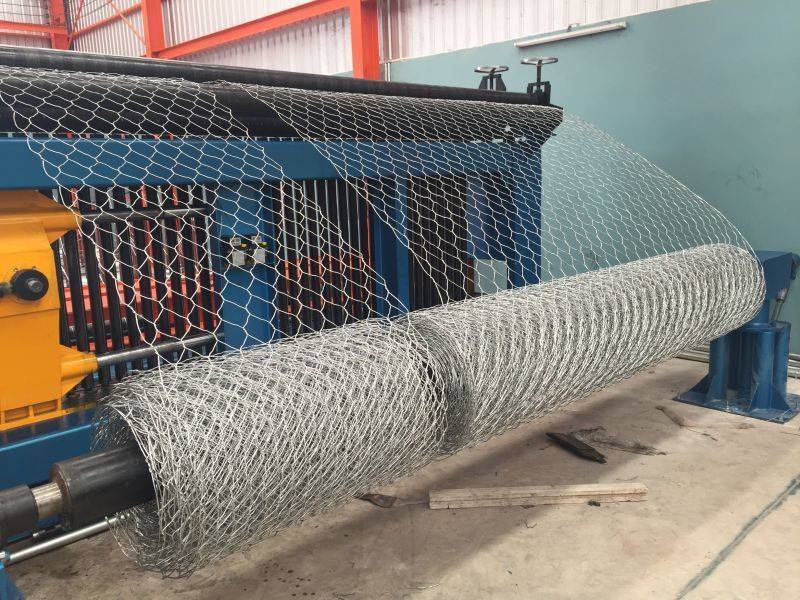
The Evolution of Stone Cage Net Machines: From Manual Crafting to Automated Production
The history of construction is punctuated by innovations that have propelled the industry forward, revolutionizing how we build and design infrastructure. One such innovation is the development of stone cage net machines, commonly known as gabion machines, which have transformed from rudimentary manual tools to sophisticated automated systems. This article traces the evolution of these machines, reflecting on past practices and celebrating modern advancements that have redefined efficiency and productivity.
Gabions—baskets filled with rocks or other materials used for erosion control, retaining walls, and military fortifications—have been around for centuries. Initially, these were handcrafted, which was labor-intensive and time-consuming. Workers would manually weave wire into nets and then fill them stones, a process requiring significant man-hours and physical labor. While effective, this method limited the speed of production and posed challenges in meeting the demand for large-scale projects.
As the demand for gabions grew, particularly for civil engineering and military uses, so did the need for more efficient production method. The first stone cage net machines were simplistic devices designed to mechanize the weaving process. These early machines were rudimentary, offering a basic level of automation that could form wire mesh but still relied heavily on manual intervention for operation and maintenance.
With the advent of new technologies in the 20th century, stone cage net machines underwent significant transformations. Engineers began incorporating automation elements, allowing for the continuous production of wire mesh with minimal manual involvement. These machines became faster and more reliable, with the ability to produce uniform gabions at an unprecedented rate.
Today's stone cage net machines represent the pinnacle of this evolutionary journey. They are equipped with advanced features such as programmable logic controllers (PLCs), touch-screen interfaces, and remote monitoring systems. Automation has been refined to a degree that allows for precise control over mesh size, wire, and dimensions of the finished gabions.
Modern machines also boast enhanced safety features, reduced energy consumption, and the ability to integrate with other production line machinery for seamless operation. Additionally, the latest models can produce various gabion types, including welded mesh gabions, to the diverse needs of contemporary construction projects.
Looking forward, the of stone cage net machines with smart factory concepts and Industry 4.0 technologies is on the horizon. This could involve the use of artificial (AI) to optimize production processes, maintenance to prevent downtime, and even robotics for loading and unloading materials. As the Internet of Things (Io) becomes more prevalent in industrial applications, the potential for interconnectivity and data-driven insights will push the capabilities of these machines even further.
The evolution of stone cage net machines from manual crafting to automated production is a testament to human ingenuity and the relentless pursuit of progress. As we reflect on the strides made, it's vital to recognize the impact these advancements have had on efficiency, safety, and the ability to meet the ever-growing demands of construction and engineering projects. With continued innovation, the future of stone cage net machine technology looks bright, promising even greater contributions to the development of infrastructure worldwide.
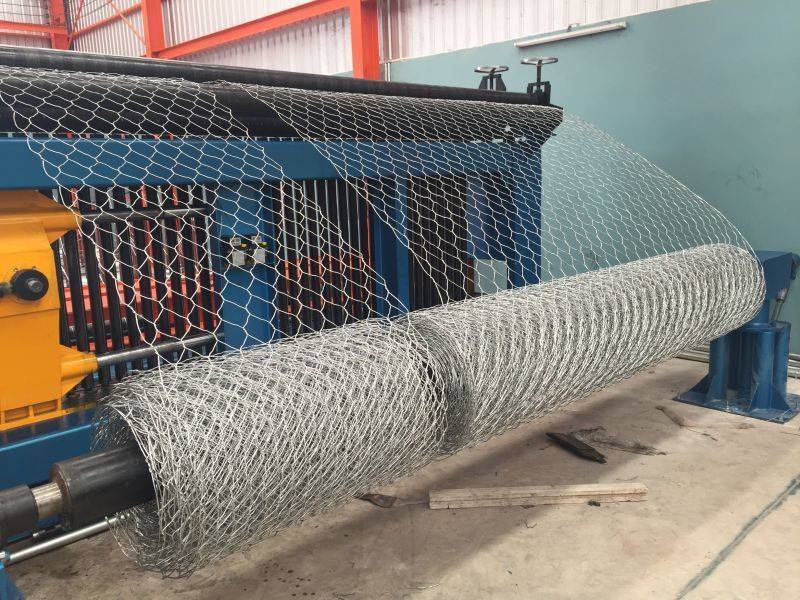